Für alle, die an unserem Deckrefit im Detail interessiert sind und die sich nicht durch den Blog mit verschiedensten Randgeschichten klicken wollen, habe ich hier eine Zusammenfassung des Projekts erstellt.
- Demontage und Wiederaufbau unseres Decks
- ungefährer Zeitaufwand
- Kosten
1.Die Vorgeschichte
Unsere Hanseat 42 ist Baujahr 1989. Ein altmodischer, aber gemütlicher (gemäßigter) Langkieler mit Mittelcockpit. Mit einer behaglichen Holzhöhle unter Deck und mit einem Teak-Decksbelag.
Wir haben unsere Atanga 2009 mit der Absicht für eine Langfahrt gekauft und waren sofort verliebt. Vor allem das Teakdeck schien uns schiffig und wunderschön. Wider besseres Wissens auf endlose Haltbarkeit und der Sinnhaftigkeit so eines Decks in den Tropen, fanden wir das besonders toll.
Beim Kauf war von der Holzdicke (ursprünglich wahrscheinlich 15 mm) noch ausreichend Material vorhanden.
Ein Fugenrefit haben wir bereits 1,5 Jahre nach Kauf des Bootes vorgenommen – nachzulesen hier
.Komplettes Fugenrefit 2010
Da während unserer Reise das Deck mehr und mehr zum Sieb geworden war, musste dringend etwas passieren. Das alte Deck sollte nach 33 Jahren getauscht werden. Statt wieder Holz zu wählen, haben wir uns für einen Kunststoffbelag entschieden. Flexiteek nennt sich das Produkt.
Wir haben den Tausch vom Deck in Neuseeland vorgenommen.
2. Das Refit – von Holz zu Kunststoff 2022
– Das alte Holz muss runter
Die alten Teakleisten sind geklebt und geschraubt. Bei unserem Deck sitzen Schrauben sowohl in der Mitte der Leisten (geschlossen mit Holzpfropfen) als auch in den Fugen. 2010 haben wir diesen Schraube – es sind ca. 2500 Stück – zum größten Teil den Kopf abgeflext, weil wir sie erst beim Fugenrefit entdeckt haben. Diese Schraubenreste verhindern, dass wir die Holzleisten mit Pressluft-Spachtel oder Multitool-Geräten abstemmen können. Uns bleibt nichts anderes, als die Leisten mit Stemm-Eisen zu entfernen.
Zunächst arbeiten um diese Schrauben herum, dann werden sie mit der Kombizange raus geschraubt. Die entstandenen Löcher bohren wir auf und füllen das neue Loch mit Epoxy (West-System mit Glue Powder 413). Das machen wir direkt am gleichen Tag, damit uns eventueller Regen kein Wasser ins Deck laufen lässt.
Eigenleistung: 200 Stunden
– Demontage der Beschläge
Alles, was an Deck montiert ist, muss runter. Bei Blöcken und Genua-Schienen, die seit über 30 Jahren nicht abgeschraubt wurden, stellt uns das zum Teil vor Herausforderungen. Die Schrauben der Genua-Schienen lassen sich nur mit einem Schlagschrauber lösen.
Um von unten an die Muttern zu kommen, müssen unter Deck Deckenverkleidungen abgebaut, Schränke zum Teil demontiert werden.
Eigenleistung: 60 Stunden Demontage, zusätzliche 25 Stunden für das Säubern der Beschläge – von altem Sika befreien und polieren
– Reparatur der Luken
Als das Holz um unsere Luken entfernt ist, stellen wir fest, dass der Rahmen der Fenster gar nicht (mehr ?) mit dem Deck verbunden ist. Zum Teil finden wir einen Spalt von über drei Millimetern. Mit einem Sägeaufsatz vom Multi-Tool verbreitern wir den Spalt, säubern und verfüllen ihn mit Epoxy (413). Die Füllung erfolgt mit einem Spritzbeutel (Zipperbeutel mit abgeschnittener Ecke) und einem kleinem Gummispachtel. Nach dem Aushärten schleifen wir die Kanten glatt.
Eigenleistung: 30 Stunden (fünf Luken)
– Deck schleifen
Zusätzlich zum Holz muss noch der alte Kleber vom Deck entfernt werden. Zuerst erfolgt dies mit dem Stemm-Eisen oder einem Abzieher. Noch verbliebene Reste werden mit dem Exenter-Schleifer und 40er Schleifpapier entfernt.
Unter dem Kleber befindet sich eine Gelcoat-Schicht. Auf Anraten der Bootsbauer der Werft soll diese ebenfalls abgeschliffen werden. Das neue Deck soll auf dem nackten GFK aufgebaut werden. Gelcoat ist so hart, dass es in angemessener Arbeitszeit nur mit einer Flex abgeschliffen werden kann (36er Korn). Dies ist wegen extremer Staubentwicklung in Neuseeland unter freiem Himmel verboten.
Wir entscheiden, dass dies in der Halle von den Arbeitern machen lassen. Allerdings bereiten wir mit dem Exzenterschleifer bzw. dem Multitool alle Kanten und Stellen vor, an die man mit der Flex nicht heranreichen kann.
Zusätzlich bessern wir Beschädigungen am GfK aus (Epoxy plus 413), die durch das Abtragen vom Holz entstanden sind. Ausbessern, schleifen, noch einmal ausbessern.
Am Ende ist das Deck glatt und eben als wir es zur Weiterbearbeitung an die Werft und zur Muster-Erstellung für den neuen Flexiteek Belag übergeben.
Eigenleistung: 90 Stunden
– Flexi Teek – Das Aufmaß
Die Erstellung der Vorlage für den Decksbelag, die Herstellung und Verlegung haben wir komplett von der Firma Brin Wilson, Auckland, Neuseeland vornehmen lassen.
Die Erstellung der Schablone erfolgte fünf Wochen vor der Verlegung. Zu dem Zeitpunkt stand Atanga bereits in einer Halle.
Die Schablone wird mit einer unelastischen Waben-Folie hergestellt, die sich wie eine zweite Haut aufs Deck legen lässt ohne zu verziehen. Von jedem Detail des Decks wird auf diese Weise eine Kopie abgenommen – die Formen, jede Biegung und jedes Gefälle. Die einzelnen Teile werden zu einem großen Stück zusammengeklebt. Viele Stunden wird nur geschnitten und geklebt. Anschließend werden auf der Folie die Ausschnitte für Luken und das Cockpit, die Winschen markiert. Sämtliche Kanten und jedes Schraubenloch für alle Decksbeschläge, die wieder angebaut werden, muss markiert werden.
Hier ist Präzision erforderlich, denn an Hand dieser Folie wird im Werk unser neuer Decksbelag gefertigt.
Arbeitsaufwand: 16 Stunden
– Deck Aufbau
Den Aufbau des Decks haben wir durch die Werft (Norsand Boatyard, Whangarei, Neuseeland) vornehmen lassen:
– altes Gelcoat abschleifen
– abdecken und abkleben
– eine Lage Glasfasermatte mit Epoxy
– Beseitigung von Unebenheiten, Spachteln (mit Epoxy und 417), schleifen, Spot Filling, schleifen, Pin Hole Filling, schleifen
– drei Lagen Interprotect (wasserdichte Sperrschicht) streichen
– Beseitigung der Abdeckungen
Kosten: Arbeitsaufwand (160 Stunden) und Material: zusammen 3900 Euro

Eine Besonderheit sind unsere Genua-Schienen – die Löcher werden mit den alten Schrauben frei gehalten, da sie nach dem Spachteln nicht neu gebohrt werden können. Die dazugehörigen Muttern sind unter Deck einlaminiert und nicht erreichbar
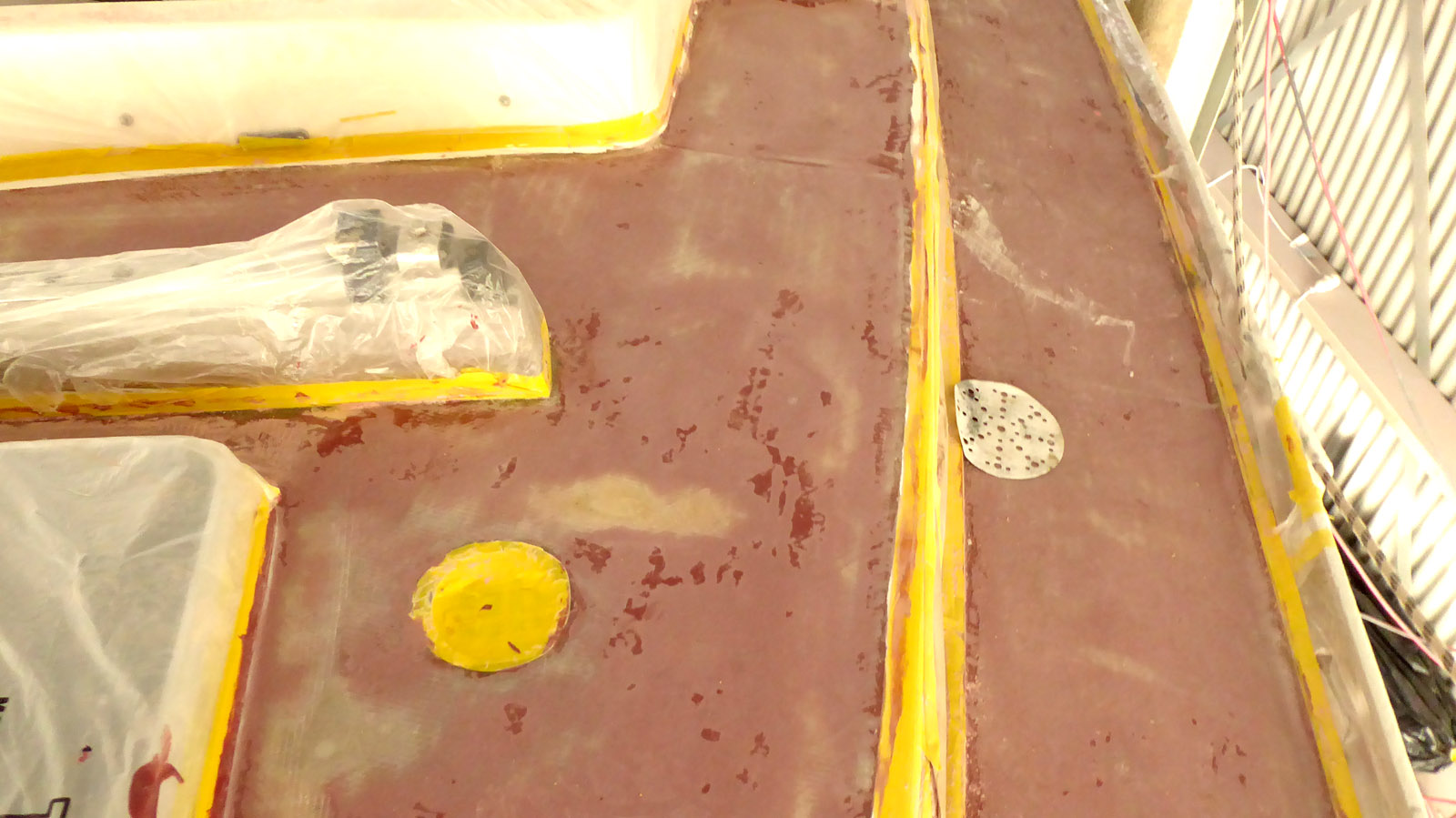
Alle Unebenheiten müssen weg – das Flexi Teek verzeiht keine Dellen oder Beulen – jede Unebenheit würde sichtbare Schatten werfen
– Flexiteek – der Herstellung
Bei der Herstellung des Decksbelages waren wir nicht dabei. Das erfolgt in der Fabrik in Auckland. Aus langen Bahnen Kunststoff (in etwa so breit wie eine normale TeakHolzleiste) wird das Deck anhand der Plastikfolien-Vorlage zusammengeschweißt. Die Verschweißung erfolgt mit schwarzem Kunststoff, was optisch einer Verfugung wie bei Holz sehr nahe kommt. Jedes Schiff ist anders, somit ist jedes Flexiteek-Deck ein Unikat.
In tagelanger Handarbeit wird der Decksbelag zusammengeschweißt.
– Flexiteek – die Verlegung
Im Grunde ist Flexiteek wie Teppich verlegen – nur etwas aufwendiger. Entsprechend wird das Deck in großen „Teppich“rollen angeliefert. Flexiteek wiegt ungefähr 4,5 Kilo pro Quadratmeter bei einer Dicke von 5 mm.
Unser Deck wurde werkseitig in drei Teilen vorgefertigt. Vom Bug an hälftig geteilt für die Backbord- und Steuerbord-Seite. Und einen weiteren Teil für das erhöhte Deck ums Cockpit herum. Nur das Stück für den Ankerkastendeckel und die Umrandung für die große Backskiste am Heck sind lose und nicht mit dem großen Teppich verbunden.
Zunächst werden die Stücke aufs Deck gelegt und mit der Heizluftpistole geschmeidig gewärmt. Anschließend wird das Teek mit Gewichten belegt, um dem Kunststoff das Aufrollen abzugewöhnen.
In langen Bahnen wird Klebeband neben den Teek-Matten auf das Deck geklebt. Darauf werden um die Matten herum – mit einer Heißklebe-Pistole – kleine Abstandhölzer befestigt. Diese sollen die Matten an ihrer Endposition fixieren. Das Teek wird angehoben, Klebstoff (Bostic) mit einem Zahnspachtel vollflächig verstrichen und mit einer Walze wird der Teek-Belag angepresst. Angedrückte Flächen werden sofort mit Gewichten beschwert.
Dicht neben die Abstandshölzer kommt ein weiter Streifen mit Vacuum Tape. Im nächsten Schritt wird eine dicke Plastikfolie über dem Flexiteek ausgebreitet und die Folie an das Vacuum Tape angedrückt. In der dicken Folie befinden sich Ventile an die eine Vakuumpumpe angeschlossen wird. Über Nacht wird jetzt der Decksbelag auf das Deck mit einem Vakuum gesogen.
Das soll nicht nur ewig (auf das Deck erhalten wir 7 Jahre Garantie) halten, sondern eine absolute Wasserdichtigkeit erzeugen.
Nachdem alle großen Teile verklebt sind, folgen die Details. Noch befindet sich eine Naht zwischen Backbord- und Steuerbord-Teppich. Diese Naht wird einfach verschmolzen. In eine Art Heißklebepistole kommt eine Wurst Flexiteek Material und diese wird in die Naht eingeklebt. Die Wulst, die übersteht, wird mit einem Messer abgeschnitten und mit 40er Schleifpapier die Naht unsichtbar weg geschliffen. Mit dem gleichen Verfahren werden die noch fehlenden schwarzen Pseudo-Fugen an den Fensterumrandungen eingeschmolzen.
Die Entscheidung, welche Farbe wir wählen, war nicht einfach. Man hat die Wahl von über dreißig Farbkombinationen. Wir haben uns für „weathered“ entschieden – ausgeblichene Teak-Optik – wie durch Sonne entstandene Patina. Unser verbliebenes Teak im Cockpit sieht sehr ähnlich aus (es sei denn, es wurde gerade frisch geschliffen).
Der Kunststoff weist eine Art Holzstruktur auf. Die Reinigung erfolgt mit Wasser und einer Bürste in „Maser-Richtung“. Hartnäckige Flecken können mit 40er Sandpapier weg radiert werden. Optisch und barfuß gefühlt, kommt das neue Deck sehr nahe an echtes Holz heran.
Die Passform ist toll, das Muster ist toll, die Farbe ist toll. Wir sind sehr begeistert.
Arbeitsaufwand Flexiteek Firma Brin Wilson: 100 Stunden;
Kosten komplett; Aufmaß, Material, Verlegung, Anfahrt und Übernachtung von zwei Monteuren: 22.700 Euro
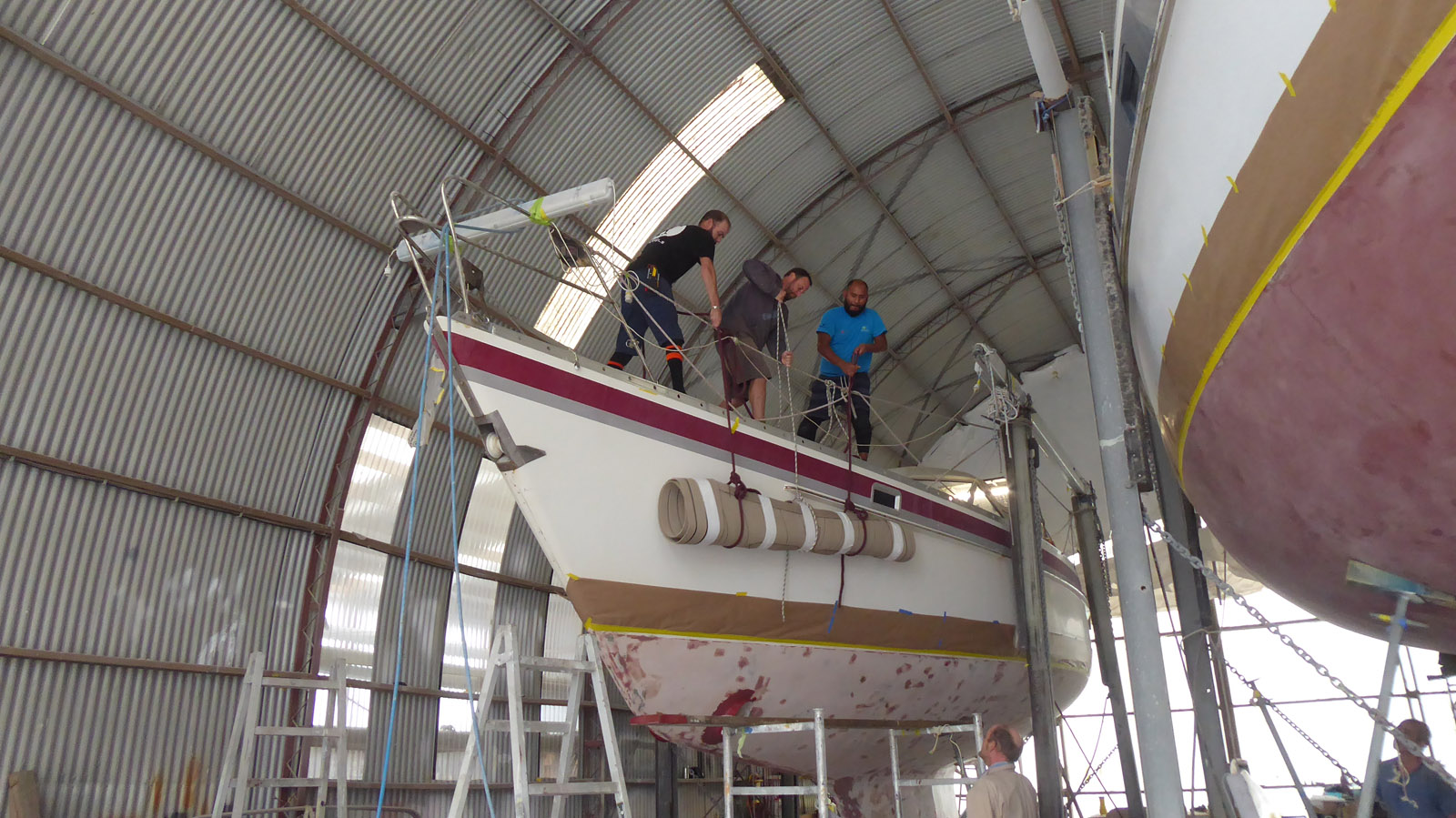
Anlieferung der Teek-Rollen

An jede Kante der Matten wird eine Reihe Hölzer geklebt, mit der das Flexiteek an seiner Endposition fixiert wird
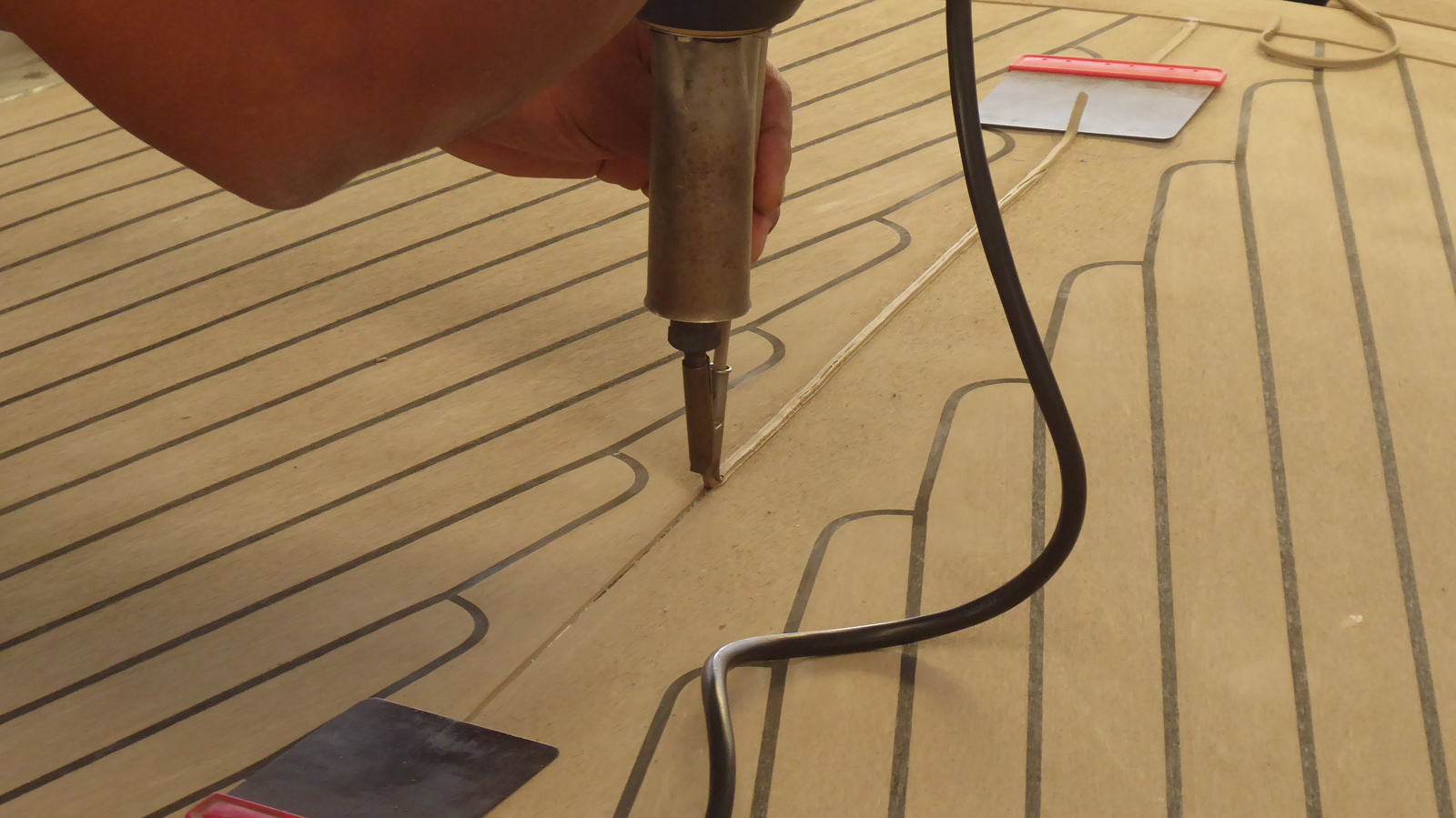
Die nun verklebten Teilstücke des Flexiteeks werden verschweißt. Hierfür wird mit einer Heißklebepistole ein Streifen Flexi-Material in die Fuge geklebt

Zum Schluss wird noch einmal die Maßfolie aufgelegt, um Löcher für die fehlenden Beschläge zu markieren
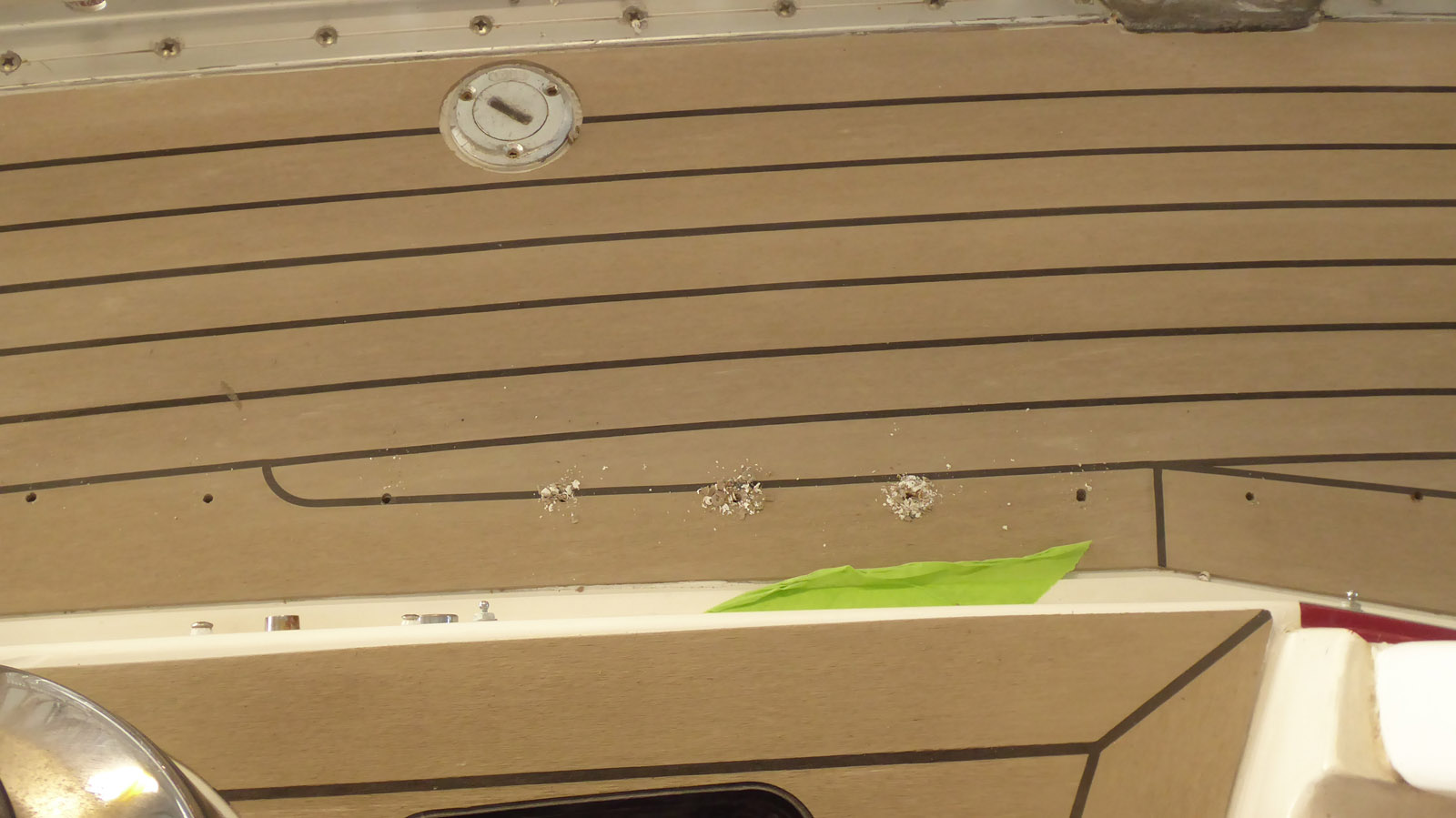
Hier die Bohrung für die Löcher der Genuaschienen – das passt am Ende tatsächlich auf den Millimeter
Re-Montage der Beschläge
Diese Arbeit wird wieder von uns übernommen. Wir hatten uns das erheblich einfacher vorgestellt. Jeder Beschlag erfordert eine individuelle Behandlung. Alle Beschläge, die eine hohe punktuelle Belastung auf das Flexi-Teek ausüben, sollen grundsätzlich nicht auf dem Flexi-Teek montiert werden.
Also müssen entsprechende Aussparungen für die Beschläge in das neue Deck geschnitten werden. Was bei den beiden Profi-Monteuren so einfach erschien, muss geübt werden. Der Kunststoff vom Deck ist zwar biegsam, aber zäh. Und es erfordert eine gehörige Portion Mut in das nagelneue Deck Löcher zu schneiden.
– Montage der Heber von den Deckeln vom Ankerkasten und der Backskiste.

mit einem stumpfen Messer abkratzen und den Rest mit 40er Sandpapier abschleifen – wichtig! immer in Richtung der „Maserung“ schleifen
Die Klampen sind am einfachsten zu montieren. Sie werden in ihrer frisch geschnittenen Aussparung direkt aufs GFK geschraubt und verklebt. Dass die Klampen jetzt 5 mm tiefer stehen und nicht mehr direkt auf dem Decksbelag, bereitet optisch keine Probleme.
Alle weiteren Beschlägen „versinken“ in ihren neuen Ausschnitten – es müssen individuelle Lösungen gefunden werden.

Beherzt ein Loch ins neue Flexiteek schneiden – leider versinken die meisten Beschläge dann zu tief in der neuen Aussparung

Durch viel Schleifarbeit entsteht so eine perfekte Scheibe von 3,5 mm. Die Epoxy-Scheibe wird in die Aussparung für den Beschlag geklebt und dieser steht dann etwas oberhalb des Deckbelags
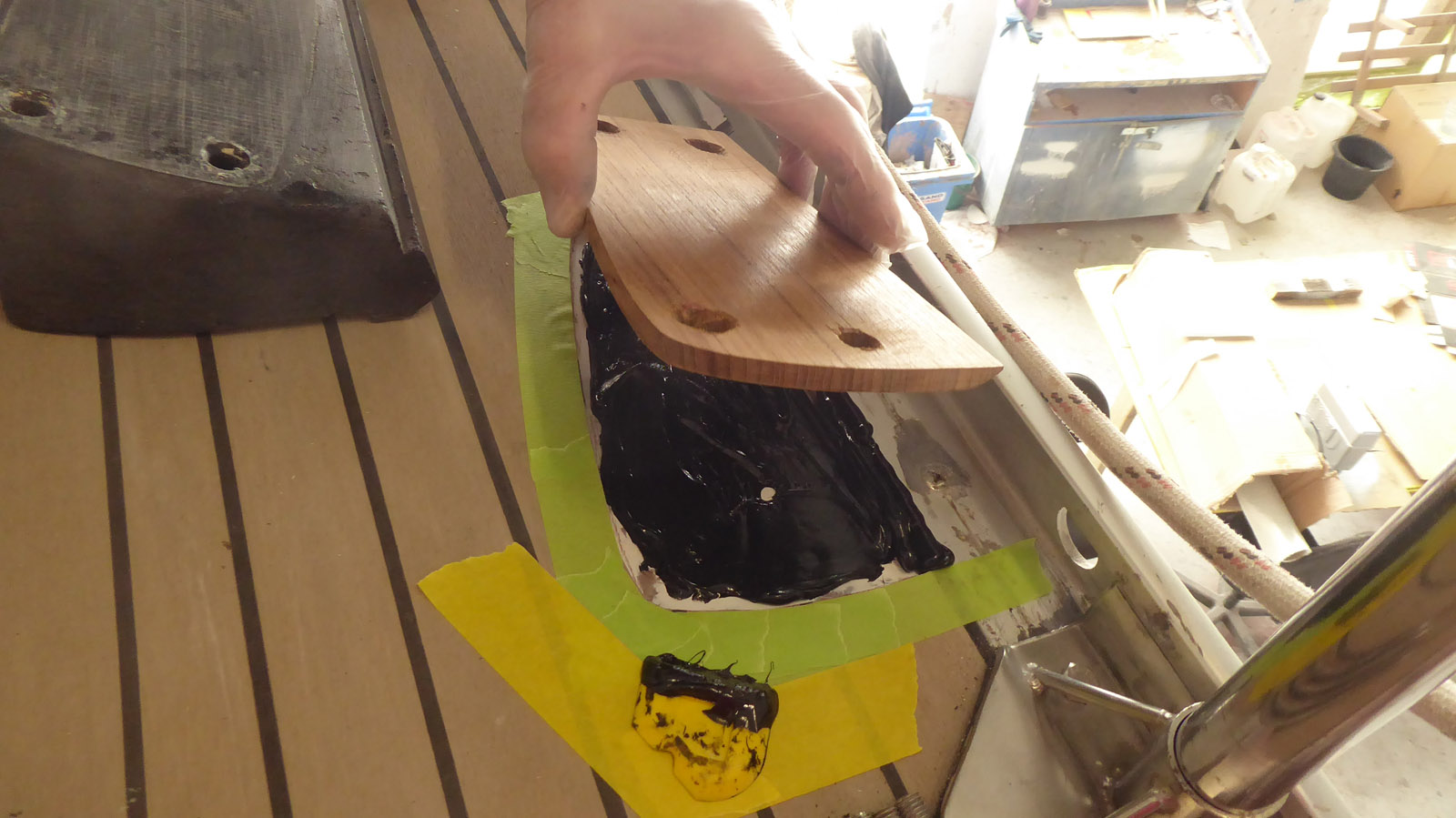
Bei den großen Umlenkblöcken für die Genua-Schoten lösen wir das Problem mit einem zugesägten Teakbrett
Dadurch, dass der neue Decksbelag nur noch 5 mm stark ist, statt früher der Holzbelag 15 mm, ergeben sich weitere Probleme. Alle Bolzen und Schrauben sind jetzt zu lang. Die meisten können nicht wieder verwendet werden, da sie sich sonst durch die Deckenverkleidung unter Deck bohren würden.
Auch unsere Relingsstützen sind davon betroffen. Die Abstandshalter, die früher die Stützenfüsse erhöht haben, sind jetzt zu flach. Hier gleichen wir die fehlenden Millimeter mit Resten des neuen Flexiteeks aus.
Ganz zum Schluss müssen noch Sika-Fugen zwischen Fußreling, um die Luken herum und am Cockpit gezogen werden. Wir haben das noch nie gemacht, aber dank vieler Tipps aus dem Internet kann sich das Ergebnis sehen lassen.
– gut abkleben
– große Mengen Lappen und Latexhandschuhe bereit halten
– die Fugen großzügig mit Sika füllen – aber nicht zu viel, dann wird es Schweinkram
– mit einem Silikonspachtel glatt ziehen (zwischen Flexiteek und Fußreling)
– mit einem in Geschirrspülmittel getränktem Finger nachziehen ( an den Luken-Fugen)
– Klebeband entfernen
– Kleine Macken oder übergeschmiertes Sika erst nach vollständiger Aushärtung entfernen bzw. wegschleifen
Arbeitsaufwand Re-Montage komplett: 220 Stunden
Eigener Arbeitsaufwand: altes Teakholz entfernen, Demontage Beschläge, Luken Reparatur, Deck schleifen und zum Wiederaufbau vorbereiten, Re-Montage aller Beschläge und Fugen mit Sika abdichten: ca. 625 Stunden
Arbeitsstunden Deckaufbau (Fa. Norsand): 160 Stunden
Kosten (Arbeitslohn und Material): 3.900
Arbeitsstunden Flexiteek (Fa. Wilson): ca. 280 Stunden
Kosten (Arbeitslohn und Material): 22.700
Sonstiges Material: 1.500
Kosten komplett: 28.100 Euro